Service Operations – The Story of Recovery
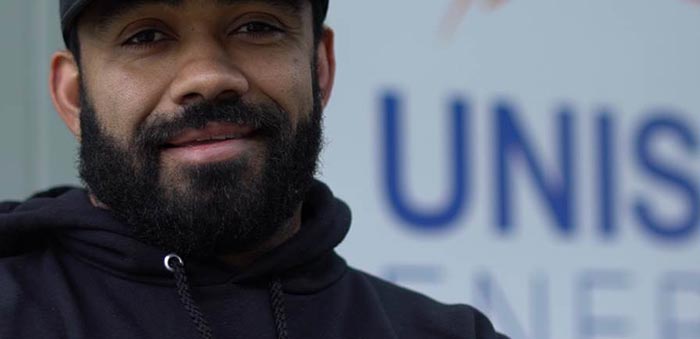
Unison Energy is frequently asked to take over existing sites with poor performance. Today, these assets average 98-99% availability.
Recognizing an underperforming site is easy. Availability or uptime metrics are below expectations, equipment failures cause lengthy delays, recurring failures are difficult to fix, and it often seems like an unending parade of one unrelated problem after another.
Every service team will be faced with underperforming assets at some point — whether at an existing site or a new acquisition — and optimizing these assets’ availability requires a strategic roadmap for returning them to optimal performance.
Below, we have put together a list of critical steps for crafting a successful turnaround program:
1. Organize and Clean the Site
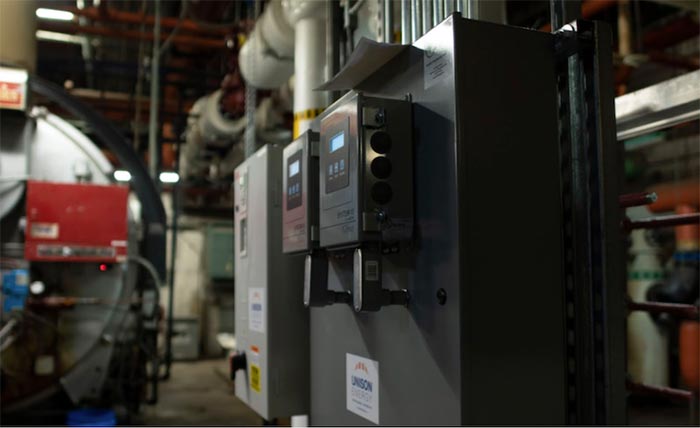
In our experience, problem sites tend to be disorganized sites. Without constant attention, a site can easily fall into a self-reinforcing cycle of disorganization. Technicians that are constantly responding to critical faults, spending long days, nights, and weekends on repairs, have little time or energy to clean up a site.
A clean site allows technicians to more easily identify minor problems before they turn into major problems — and to respond to these minor problems quickly. If a site as a whole is dirty or messy, a small drip in an oil line can easily be missed until the equipment becomes damaged. Conversely, at a site that is kept spotless, any leak quickly becomes apparent. This is the only way to get ahead of problems and avoid always playing catch-up.
Therefore, any turnaround at Unison Energy begins with a trip to the hardware store for storage and cleaning supplies. Then, tools are organized, spare parts are cataloged, labeled, and stored using our inventory system, equipment is wiped down, trash is thrown out, and cleaning supplies are stocked. Simply put, every day should begin and end with site cleanup.
2. Review the Site’s Historical Data
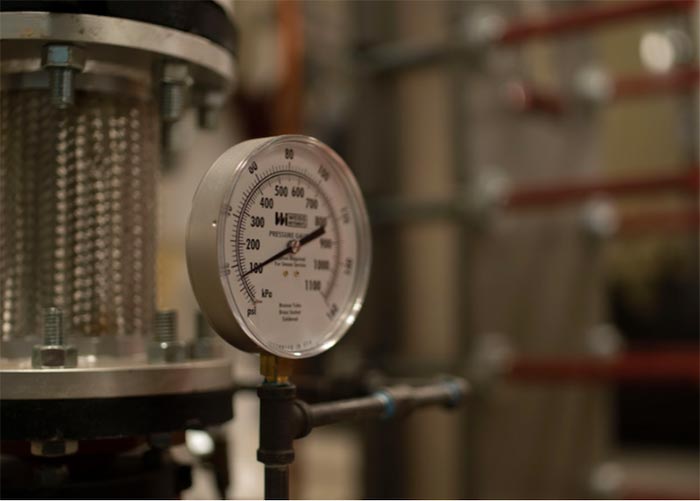
Systems that break down frequently rarely do so by chance, but to understand an issue, service teams need to have access to the right data. Unison Energy captures 50-80 million data points per day at each site, including inlet temperatures, exhaust flows, and everything in between. We use this data to identify recurring issues and the operating characteristics that lead up to these issues.
We find that gathering as much historical data as possible on a site can help you identify issues and prioritize an action plan. Written logs, parts ordering histories, and interviews with technicians, operators, and even the finance team can shed light on critical patterns in site performance.
3. Identify Recurring Issues and Resolve, Predict, or Minimize Them
For a period in 2019, we were beset by recurring issues with cracked pistons in one of our engine classes. Each event caused 1-2 weeks of downtime as we waited for the parts to be delivered, the original equipment manufacturer (OEM) to have a technician available, and the hydraulic press required to replace the part to be shipped. The repair itself then took 4-8 hours of hard work.
After inspecting the failed parts, we determined that the problem was cylinder heads that were wearing prematurely and causing the pistons to crack. By partnering with the OEM, we were able to plot a course of corrective action. Over a number of months, we focused on three steps:
- Predict Failure – Although the recommended interval for measuring cylinder headwear was 2,000 hours, we began measuring every 250 hours and noting trends. This allowed us to predict when the heads would fail ahead of time and stock parts, schedule technicians, and prevent long outages.
- Minimize Impact – To minimize downtime, we began stocking both parts and tools on site. We worked with our equipment partners to provide training to our technicians and secure authorization to perform warranty work on specific parts. This allowed us to reduce downtime from weeks to a day or two.
- Resolve the Issue – The final step was to work with the OEM to replace the cylinder heads with an updated release that was less prone to wear. This was a multistep, multi-month project. First, we needed data showing that the heads were consistently wearing ahead of schedule; our measurement logs from more frequent testing proved to be invaluable in identifying this trend. Second, the OEM had to design and test a new version of the cylinder heads. Although it took time, the change was a success for our clients, the OEM, and our equipment provider.
As this example illustrates, even recurring problems that stem from OEM-issued parts can be resolved over time. OEMs hear all manner of problems blamed on them every day, but providing them with the data they need to document a fault on their part goes a long way toward gaining their support in resolving the problem. Unison Energy is fortunate to have a fleet of systems that enables us to see trends as they emerge. Companies with only one or two of a given equipment type may best be served by joining (or creating) a user group to compare notes.
4. Catch Small Problems and Resolve Them Right Away
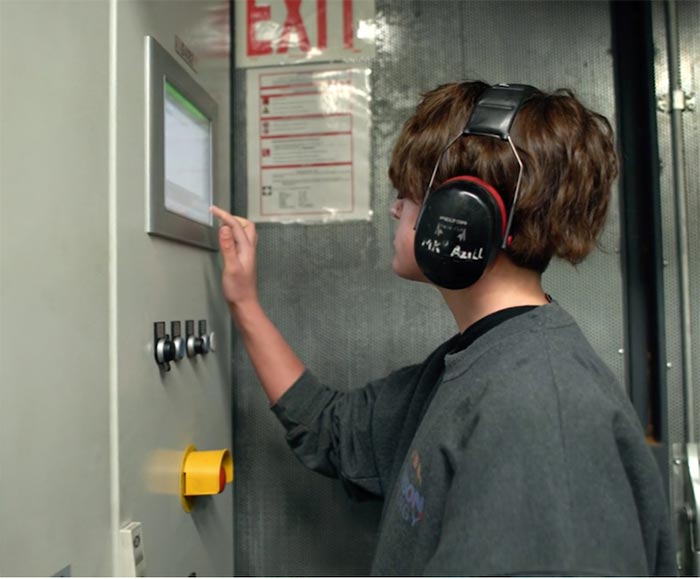
A focus on large, recurring issues is necessary for a site turnaround. However, many service leaders are frustrated to find that even once they have addressed these issues and improved availability, their site still lags. That is typical because many seemingly small issues continue to take equipment out of service.
A well-run site addresses small problems immediately — before they turn into large problems. Every site visit needs to involve looking at the site, listening to the equipment, and smelling for unfamiliar odors. Technicians need to identify drips before they become leaks, worn parts before they become failures, and vibrating equipment before it shakes loose and causes damage. Once this becomes a habit, the site is well on its way to operating optimally.
Whether it is taking the time to investigate an unknown vibration, ordering a part and requesting support for a minor leak, or calling the utility for a faint smell of gas, our technicians are encouraged, trained, and authorized to take initiative to fix problems immediately. They are provided with corporate credit cards to make purchases to resolve issues immediately and are empowered to operate their sites as needed.
5. Invest in the Site
Owners need to recognize that all of the work covered above comes with a cost. It requires an investment of time to bring in additional team members and operations leaders, money for spare parts and repairs, relationships with equipment vendors and OEMs, and effort to go above and beyond normal workloads to get the site back on track.
When a site is disorganized or inefficient, everything takes longer than it should. Faults occur more frequently, and because troubleshooting is not optional, technicians end up working long days, every day. Bad habits can sink in and small issues go overlooked in favor of larger, more immediate problems.
But with the right investments, any service team can be proactive about optimizing its strategies through the steps outlined above. Although the process takes time, it ultimately ensures a better work-life balance for technicians, which tends to mean better performance. With fewer callouts and shorter repair times, technician response time improves, which translates into better uptime.
Recovery Is a Process
The road to recovery will inevitably have obstacles, even if you are taking steps toward improving uptime. Change does not happen overnight. Optimizing a site can take months, but with a clear plan in place, it will happen. Deploying digital tools is helpful as long as you have the other building blocks in place: organization, leadership, a well-designed workflow, and technicians who are trained and empowered to solve problems. For Unison Energy, the result has been better visibility, a more committed crew, and 98- 99% uptime that exceeds the industry standard.
At Unison Energy, our service operations process is designed to ensure high levels of uptime so that our customers enjoy the full benefits of our microgrids. If you’re interested in learning more about how Unison Energy owns, operates, and maintains microgrids, click here to contact a Unison Energy sales representative.
Energy insights, delivered
Subscribe for more content.