Unison Energy’s Four-Step Approach to Industrial Power Retrofits
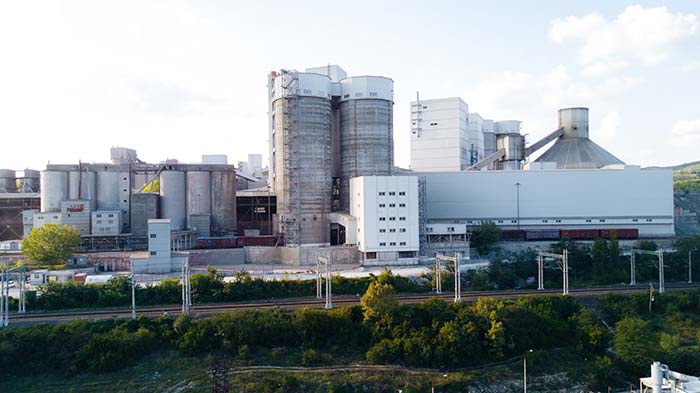
Industrial sites have unique requirements for on-site power generation. Unison Energy takes these specific needs into account at each step of the process.
Retrofitting industrial facilities with combined heat and power (CHP) systems offers cost savings, improved resiliency, and reduced emissions. However, properly implementing new equipment and systems at these large, complex sites – which often have unique and potentially challenging power needs – requires an experienced and knowledgeable team to ensure the project’s success.
At Unison Energy, Dan Samek and Brian Mefford, Senior Project Managers of Turbine & CHP Projects, are experienced in leading industrial-sized projects: throughout his career, Dan has worked on a total of 13,601 MW over 20 projects, including military and power projects, while Brian has handled 1,200 MW over 39 projects, including large food manufacturing sites.
Based on input from their decades of experience, we have developed a four-step approach for designing, building, and operating CHP-based microgrids for industrial facilities.
1. Perform a Feasibility, Complexity, and Initial Cost Assessment
Existing industrial systems and other complications can make the initial assessment and design process more challenging.
Unison Energy evaluates each site’s current infrastructure, including electrical and gas tie-ins and viable locations for the CHP system equipment. This process involves a full feasibility study and coordination with contractors to determine the approximate complexity and estimated cost for outfitting the plant.
Many industrial sites are brownfield projects, which require a more flexible design and build process than greenfield facilities. Implementing new natural gas piping, gas handling, and emissions-reducing equipment can require extensive modifications to existing infrastructure. For example, Dan worked on an upgrade project at a large power plant that required the engineers to conduct extensive surveying and site modifications in order to reroute the existing utilities and install the new equipment, including a large structural pipe truss and new silos – all without disrupting normal operations.
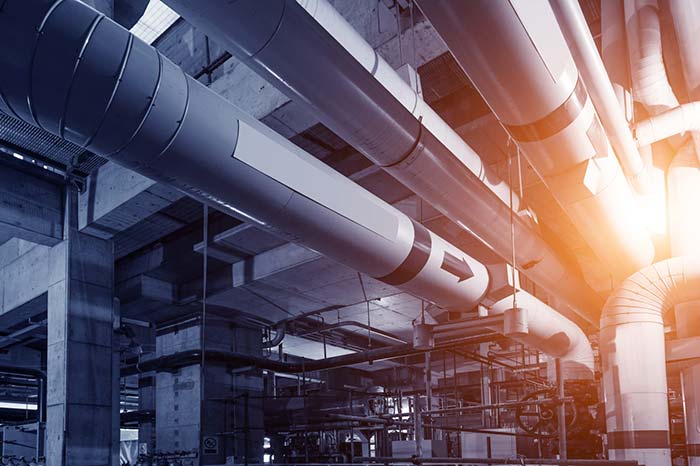
2. Take a Detailed Approach to Integrate New and Existing Systems
For a successful retrofit, each detail of engineering and aesthetics must be taken into account.
Once it is established that the project is feasible, Unison Energy takes a meticulous, in-depth approach to mapping out the rest of the project – which is especially critical when a site requires major retrofits.
New systems must be able to integrate with decades-old legacy equipment or a site’s preferred vendors or brands, which can require extensive engineering. Industrial sites may also lack the physical footprint needed to easily install new equipment. Getting the retrofit process right requires close attention to details of the plant’s operations.
Industrial sites often require extensive redesigns to ensure the new equipment will integrate and operate successfully. Brian worked on a project that involved a natural gas pipeline supplying several power plants in Bakersfield, CA. He helped retrofit a low-pressure steam system on each 50 MW Steam-Inject Gas (STIG) turbine, and in the process, the controls system had to be completely redesigned (from the control room to each well site) to ensure it could integrate with the newer equipment. Further, this retrofit required completely reengineering the piping and expansion systems, pumps, electrical, and controls.
As part of our detailed approach, we also take the time to match the aesthetics of a plant’s existing masonry, brickwork, landscaping, or retaining walls with precision. One previous client could not tell where an old plant structure ended and the new power equipment was installed because of the thoroughness of our team’s work. The equipment was also hidden from view from a public road and had sufficient acoustic baffling to render it undetectable from the adjacent parking lot.
3. Design and Upgrade to Meet All Codes and Standards
It is critical that on-site power generation complies with all relevant regulations – which can be extensive at industrial facilities.
Industrial sites are subject to more stringent regulations, including ASME and state or local codes. Unison Energy’s approach takes the complexity out of our clients’ hands. We design and conduct quality inspections on our piping systems and equipment, and pressure test all of our systems to the ASME Boiler Code and Power Piping standards or to the applicable Process Piping standard.
Unison Energy also upgrades code standards for our clients. Even with plants that have been grandfathered in, we maintain compliance with current construction codes and standards like AWS, ASME, IBC, and AISC, as well as local codes, and NFPA for fire protection. Our engineers work directly with the utility to ensure that protocols are followed, and we verify our work through partnerships with independent third parties and consultants. Brian has previous experience in this area: at the Kern Mojave Pipeline Project in Bakersfield, CA, he worked on retrofitting a 16-mile natural gas distribution system for Destec Energy, interconnecting eight LM5000 STIG and two Combined Cycle Power (CCP) plants. The design adhered to all relevant ASME, API, and state codes.
Our systems are already designed to meet and exceed client and industry standards. Our equipment is certified for low emissions and undergoes rigorous compliance testing. Our insulation methods do not just improve thermal efficiency, they also mitigate the acoustics of the equipment, which means we can ensure low vibrations and sound absorbency, especially in rare cases when a facility is near residential housing.
4. Design for Operational Accessibility, Safety, and Ongoing Efficiency
On-site energy systems need to be built with operations and maintenance in mind to ensure high levels of uptime.
Throughout the industrial retrofit process, we are mindful that our systems will continue to operate for at least the next 15-20 years. We plan ahead to meet the accessibility needs and safety concerns of operational and maintenance personnel. Our internal operations team is involved in the design process, reviewing safety handrails or anchors for fall protection tethers, requiring safe access solutions, and ensuring sufficient space around equipment. If operators cannot easily and safely perform preventative maintenance, the systems are more likely to experience long-term failures or problems.
We also install new monitoring technology during construction, allowing us to remotely monitor system health and performance, which further enables us to perform prompt preventative maintenance with a minimal impact on the plant’s operations. Our operations-focused approach has enabled us to deliver a fleet-wide average of 98% uptime for our CHP systems across the U.S., even reaching 99% in recent months.
There is mutual benefit to high uptime levels: our clients need to be operational around the clock and trust our systems, and because Unison Energy owns the microgrid system, we only make money when we’re producing electricity and therms. Simply put: it is in our self-interest to maximize our clients’ uptime.
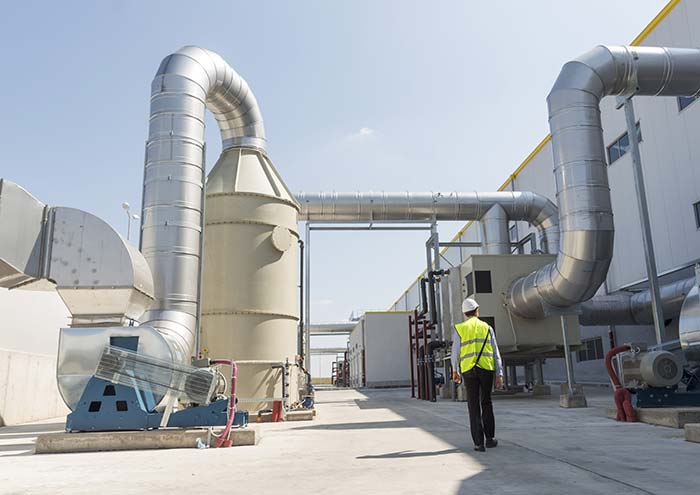
Unison Energy Brings Experience to the Table
This comprehensive, multi-pronged approach is how Unison Energy is able to meet our clients’ needs, deploy solutions, and ensure the efficacy of our retrofits and power generation solutions.
Our team has experience in industrial and clean energy systems, including natural gas turbines and reciprocating internal combustion engines, steam systems and boilers, solar PV, battery energy storage systems, and other solutions. As a whole, the team has more than 100 years of distributed generation experience and has designed, built, and commissioned over 15 GW across over 350 projects, along with 14 GW of utility-scale generating plants across 22 projects.
Further, we finance our projects under a 15 to 20- year energy services agreement (ESA) that requires no upfront costs to our clients. We work to further reduce long-term client costs by leveraging tax credits, state grants, and local utility rebates. We are prepared to implement microgrid solutions for industrial facilities of all sizes that provide greater operational control, cost savings, improved resiliency, and a lower carbon footprint.
If you think your industrial site could benefit from on-site power generation, click here to contact a Unison Energy sales representative.
Energy insights, delivered
Subscribe for more content.
Related Blogs

The Energy Crisis in Healthcare: Mitigating Financial Losses Through Reliable Power Solutions
Electricity Billing 101
Reducing Scope 1 Emissions Through On-Site Generation