Service Operations – How Culture Drives Higher Uptime
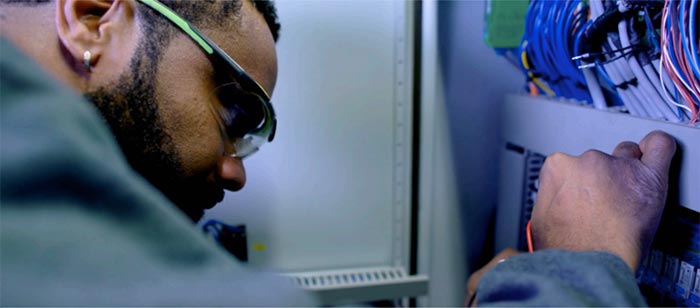
Unison Energy’s industry-leading uptime of 98-99% is possible thanks to a model where technicians are responsible for their sites and encouraged to take initiative to solve problems.
Unison Energy’s operations team consistently exceeds industry performance in asset availability, reaching 98-99% availability in an industry where 92-95% uptime is considered a well-run site. These numbers don’t happen on their own. Maximizing asset availability is more than following preventive maintenance schedules and responding quickly to issues; it requires a culture of ownership and dedication from our field service team.
Unison Energy recruits technicians that can act on their own and take initiative. We train and empower our team to take ownership of their sites, notice the small things, and fix them before they become a problem. Our team leaders train our technicians on five key principles that ultimately drive higher uptime.
1. Take Pride in Ownership
Too many service operations firms send out technicians only to make specific repairs then move on to the next job as quickly as possible to maximize billable hours.
The culture at Unison Energy is different. Our service model begins with ownership: each technician is responsible for specific locations (and cross-trained to ensure every site has extra coverage), thus each is deeply familiar with the site systems and checks on them daily.
We begin by teaching our technicians how to keep a site clean and well-organized. Like new recruits in the military being taught to make their beds, technicians learn to take pride in a clean site. This sense of ownership influences how technicians approach maintenance and ultimately determines how the site performs.
2. Actively Observe and Inspect Your Site Every Time You Visit
Unison Energy trains our technicians to use all their senses when doing daily inspections. Recently, one of our technicians was on site in Long Island. Approaching the site, he was actively looking, listening, and smelling. The technician smelled gas coming from the exhaust stack and immediately called the gas company emergency hotline. The issue with the utility’s regulator turned out not to be dangerous, but it could have become a safety issue if the leak had expanded or the gas had accumulated.
Technicians systematically inspect the entire system, beginning as they approach the unit, listening for strange noises, looking at parts and components, and smelling for wear and tear. They follow a mental checklist but also check every subsystem and component on the programmable logic controller (PLC), which displays a wide range of data points, such as engine temperature, gas pressure, gas consumption, and actuator engine cooling or gas mixture levels. Technicians check this system multiple times per day, whether remotely or on site, and use the trend data and logs to see differences that could signal an issue — small or large — that needs to be addressed.
3. Fix the Small Problems Immediately
At one of our New Jersey sites that has two reciprocating engines, one of our technicians recently noticed a compensator leaking at the rate of one drop per minute. While the leak seemed minor, the technician immediately had a compensator shipped from a Long Island location to the New Jersey location and called for support. Together, our team installed the equipment overnight while the site electrical load was low enough to run on only one engine.
The next day was 95 degrees. High temperatures and more pressure on the original compensator could have led to both engines going down for hours, costing the client thousands of dollars in peak demand charges from the utility on one of the hottest days of the year. This is just one example of how fixing small issues prevents lengthy outages that add up to significant downtime over the course of months or years.
4. Take Initiative
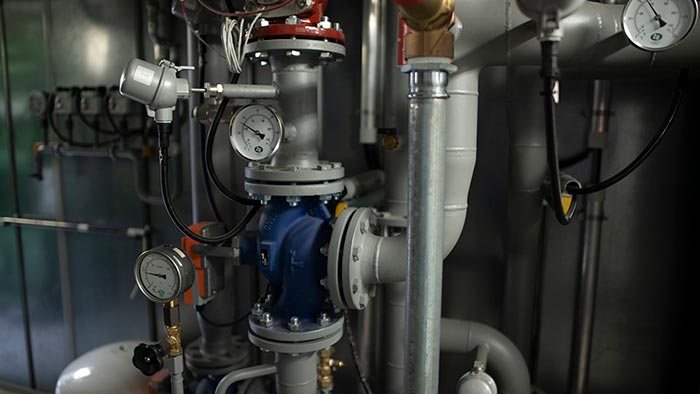
Last month, one of our technicians heard an engine vibration that simply felt different from the norm. Vibrations are not uncommon issues, and the problem might be as small as a loose plate or a broken screw, but it’s critical to investigate any changes.
In this case, the technician considered that the vibration might be due to a change in the operating mode, as a load-following engine may fluctuate often and cause vibration. Prior to shutting the engine down to look for a loose or broken part, the tech took the initiative to perform vibration analysis, running the engine at different loads to figure out when it started vibrating and comparing readings versus the baseline. Effectively, the issue was attributable to the operating mode, and the technician’s initiative prevented unnecessary downtime.
Whether it is taking the time to investigate an unknown vibration, ordering a part and requesting support for a minor leak, or calling the utility for a faint smell of gas, our technicians are encouraged, trained, and authorized to take initiative to fix problems immediately. They are provided with corporate credit cards to make purchases to resolve issues immediately and are empowered to operate their sites as needed.
5. Everybody Leads
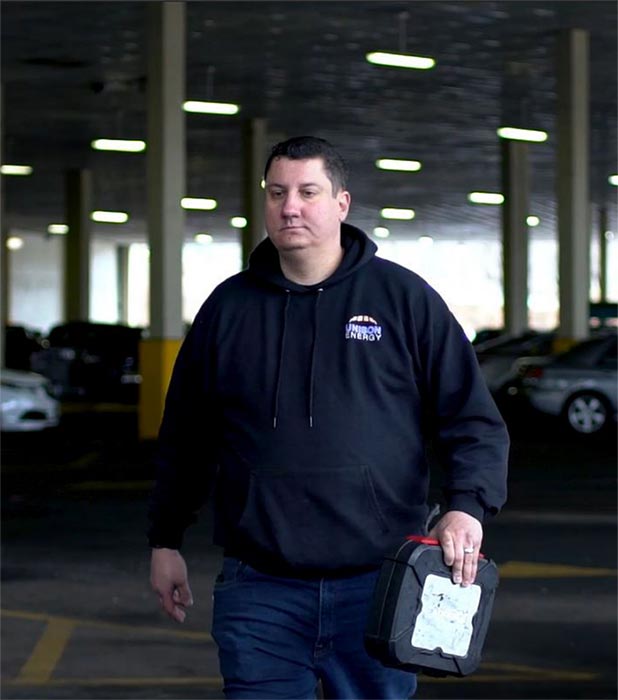
However, taking initiative goes beyond fixing pressing issues at sites. Our technicians are also trained to raise issues that impact the overall effectiveness of our team and contribute ideas on how to improve. Unison Energy does not have a corporate procedures-writing team. Our technicians are our team.
In addition to operating sites and performing equipment maintenance, our technicians write our standard operating procedures (“SOPs”), influence technology investments, inform inventory levels, write safety programs, and create and teach our training courses.
Technicians are authorized to take action immediately at the site. They have an expense limit that does not require prior approval, which means they can order parts, run to the nearest electrical parts store, or just purchase supplies because they are best positioned to know what will keep the site at optimal operational efficiency.
Because Unison Energy technicians are responsible for sites and not billable hours, they are salaried and receive quarterly cash bonuses based on uptime, which rewards the team for preventive maintenance and response time — which is also aligned with our clients’ needs. This is in direct contrast to the ineffective break/fix model, where repairmen are paid only when an issue occurs and managers are judged by technician billable hours.
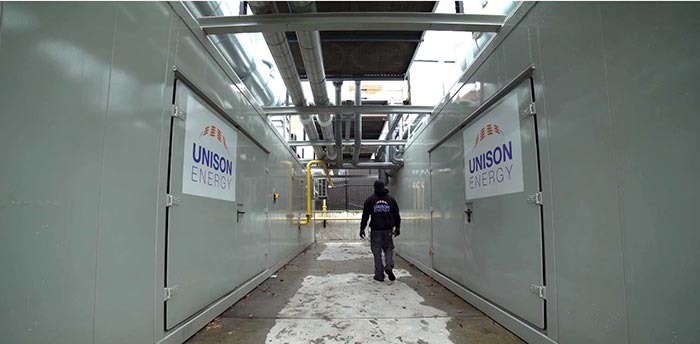
A Proactive Approach Makes All the Difference
At Unison Energy, our entire service operations team takes a proactive approach to ensure asset availability of 98-99% across our fleet. Technicians are deeply familiar with their sites, which means they can better catch and address small problems that could turn into big problems. They also take ownership of their sites, undergo thorough training, and have the freedom to take initiative to solve problems.
Thanks to the professionalism and dedication of our team, our clients enjoy asset availability that outranks our competitors.
The Unison Energy service operations model is designed to ensure your facility experiences industry-leading uptime. Click here to contact a Unison Energy sales representative.
Energy insights, delivered
Subscribe for more content.